Why QMS is so much more than a Manual
Quality Management and Quality Assurance are vital in all industries, not just aviation. For those not formally introduced to QM and QA, it can be tough to know where to start. Or how deep the rabbit hole goes.
ISO 9001. QMS. PDCA. Lean. Six Sigma. It’s a confusing world out there. You’ve googled QMS and Quality Assurance and even downloaded a few PDFs you might just copy and paste…. Well stop right there.
If you are just trying to mimic a QMS manual with your company’s logo on it, you might need to just move along. QMS or QA has no shortcuts and so should it. If you are genuinely trying to focus on the solution to what a good QMS could be? Then read on.
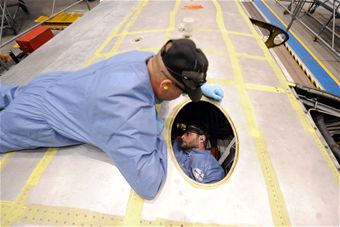
What you need right now
QMS requires that you understand one simple thing. Everything. That’s right, if you want to implement Quality Management, you need to know what the hell you are doing in the first place.
We are not going to say QMS is quick and easy, but what we will say is that you will learn the most about your business, or any business when you run it through a QMS or QA program. The Specific area we need is the AS9100, including ISO 9001: 2008 changes. This also Includes defense.
Quality Assurance (ISO)
Go now to the ISO site and bookmark that page. You will need it later – when you check your own industry, your sector, or the exact ISO number you need for a particular function.
And then I want you to click on the following ISO resource which is a free document and gives you the 7 quality management principles.
The 7 Quality Management Principles
1. Customer focus
2. Leadership
3. Engagement of people
5. Improvement
6. Evidence-based decision making
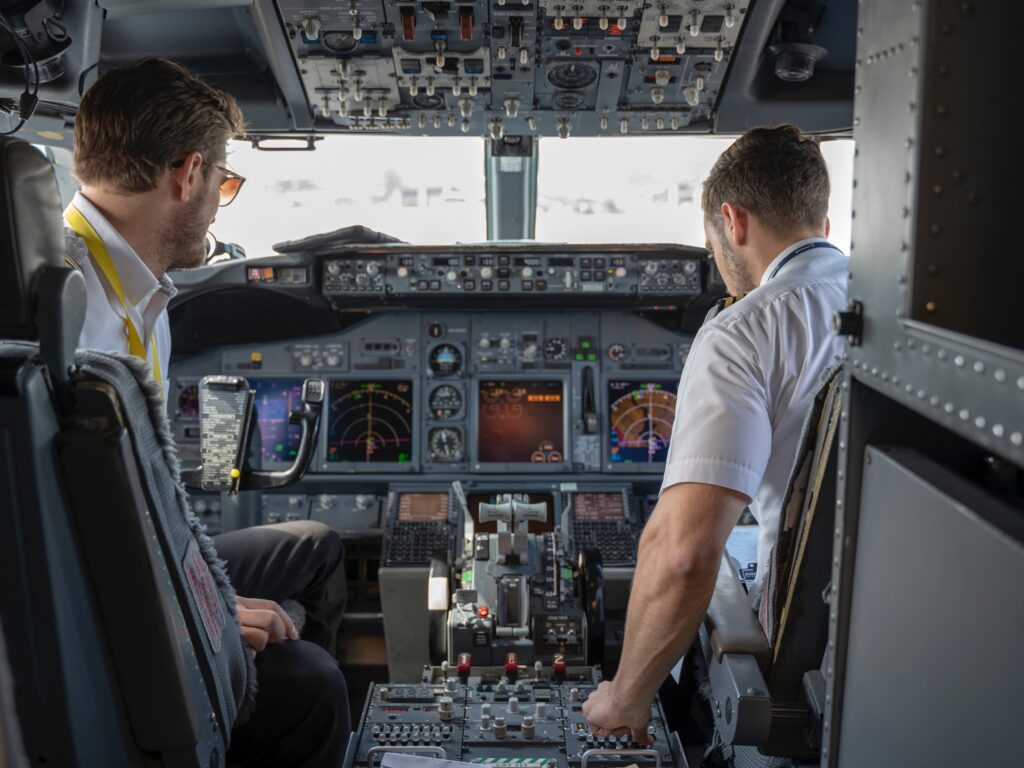
Whatever you do, or write or organize, it should have these chapters, modules, or elements. So, if you do come across a PDF Manual or your company has one, this is what you should see. If you don’t then you’re off and need to start from the beginning.
But we can simplify this further into two baskets.
1. Customer Value (points 1, 4, 5 & 7)
2. Elimination of waste (2, 3, 5 & 6)
What is QMS?
QMS should focus on customer value stream mapping (Basket 1) and then try to eliminate waste and make production as lean and accurate as possible (Basket 2). So you will survive in competition and market shifts. In fact, these are also the two core elements of “Lean”, so we know we are on the right track.
If you need a QMS, you are going to need Lean. And if you need a formal approach, you will need to get a Lean Diploma and/or an ISO 9100 Auditors qualification. Both are short courses – but their power to weight ratio is enormous.
After you’ve done these courses, you will find a whole lot of your life getting streamlined as you understand and implement efficiencies all around you.
Lean thinking & Six Sigma
Lean & Six Sigma are two separate avenues to the same place. Purdue University in the US has a good article on the subtle differences and where they originated. If you need to know the difference, read this.
Also, if you do a Diploma level in either you can consider yourself a lean “Black Belt” and don’t be told otherwise. The other side is that your employer will be delighted. I mean who wouldn’t want their staff getting into the practical details of improving the customer value path and getting processes nailed down tight.
But it’s not as easy as it sounds. You need to be good with those people to whom you will poke and prod and give directions. That’s why Lean and Six Sigman focus heavily on leadership and engagement of people because that’s exactly what you will be doing in QMS. But if you have eyes for middle or upper management, then this is the best way to work, in any sector.
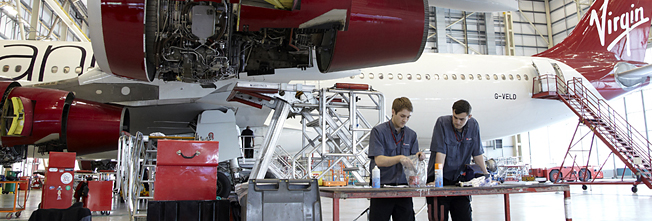
QMS Tools you need to master
- VSM or Value Stream mapping
- Flowcharts
- Standard Work
- The 5s
- Fishbone Diagram