WingZer0
Aviation Sustainability
Aviation Needs You!
All of you.
Aircraft & Engine Designers, System Designers, Pilots, Air Traffic Managers and Passengers. Folks in the Sustainable Aviation Fuel sector, the Battery technology, and the Hydrogen Fuel sector.
We all have a role to play and while some will contribute more than others, just like taxes, it will be passengers voting with their wallets who will make the difference.
Historically, aviation has been slow to adopt modern technologies. We blame it on the regulatory environment and sometimes we are right. But the time for inaction has long passed. We’ve got a mere 23 years to change the business so fundamentally that it will be reinvented entirely.
Or it could be the end.
But we have the tools and the talent to do it. And we have the organizations and associations working together toward this goal. How are we going to do it exactly? Read on.
What is #NetZero 2050?
There are a variety of organizations and associations that are guiding us to net zero. Below is a useful timeline with links to the key pages for each agency and their contribution.
Aviation is a sophisticated industry overseen by extensive regulatory structures. To deliver the technological advancements by 2050, change, innovation and investment needs to happen today.
This page hopes to achieve two things. First, to give you a brief overview of the pathways we will use to achieve our goal of zero emissions. And second, to show you areas where we need to focus our attention, our talent, and our ideas.
Our Pathway to net Zero Emissions by 2050
The "Lasagna" Graph
If you are new to the NetZero 2050 Journey, let me introduce you to the ATAG “Lasagna” Chart. Widely considered to be the agreed combination of solutions that will deliver sustainability to the Aviation Industry. As you can see in GREEN, Sustainable Aviation Fuel plays an enormous part.
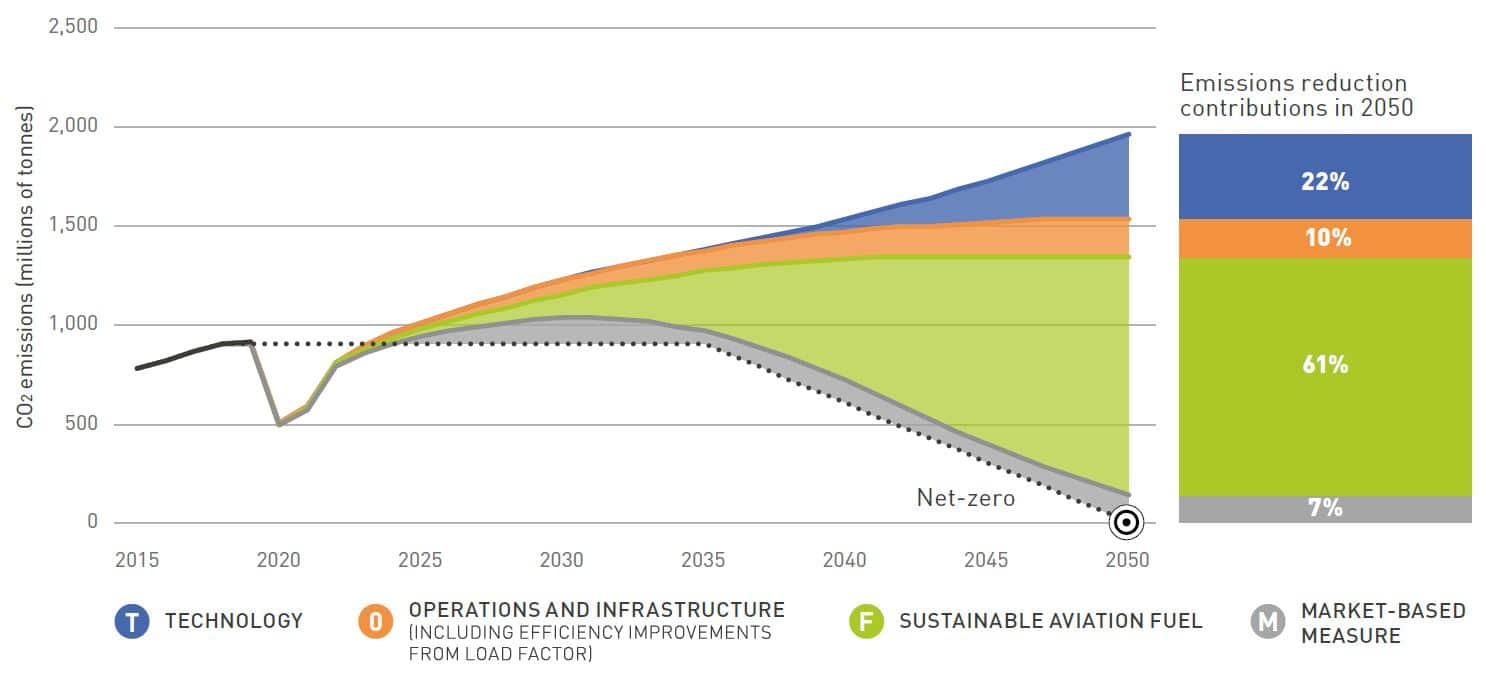
Sustainable Aviation Fuel (SAF)
What is "Drop in" Fuel
Aviation Fuel is JET-A1, or kerosene derived from fossil fuel (Oil). SAF is still Jet A-1/Kerosene but derived from non-conventional sources that are renewable. BIOFUELS being an example.
SAF is a drop-in fuel because it is chemically and physically identical to current fuel. This is key because.
- We can mix it with current fuel (to varying degrees)
- We don’t need to change the current to-plane delivery infrastructure.
- Current aircraft and engine technology does not need to change.
And to call this “Sustainable” Aircraft Fuel it must meet criteria such as lifecycle carbon emissions reduction, limited fresh-water requirements, no competition with needed food production and cause zero deforestation. So SAF consists of Three Key elements
- Sustainable
- Alternative feedstock to crude oil
- (is) Fuel
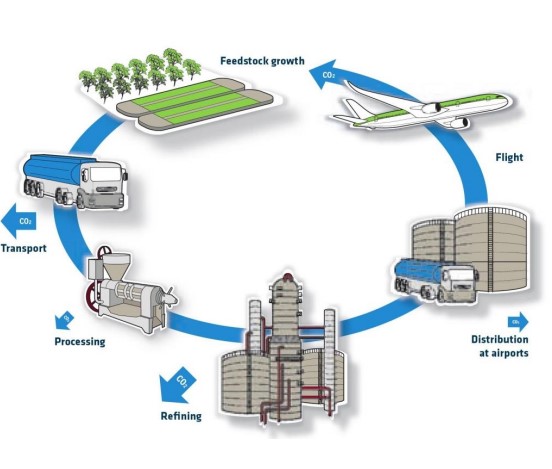
Watt-hour per Kilogram
Let’s get a little scientific. It’s important when understanding energy to fly aircraft. Specific Energy Density (SED) is measured in Whr/kg and is our best way to understand the energy storage capacity of a substance. Let’s look at the current aviation fuel sources.
- Lithium-ion battery SED 250 Whr/kg
- Lithium-ion battery (in 2030) SED 850 Whr/kg
- Aviation Jet A-1 fuel SED 11,900 Whr/kg
We want to get to this subject quickly. As it is potentially the best replacement for aviation fuel in the future. PtL extracts carbon from the atmosphere using an electrolyte process.
Feedstocks are therefore unlimited, but production is tricky and expensive. But where PtL lovers are optimistic is as other industries improve their sustainability (and reduce their requirements on raw materials), it makes Ptl more economical. Airbus have a PtL explainer page if you want a deeper dive.
Aircraft must carry the fuel it uses. So, while it sits in the fuel tanks waiting to become propulsive energy, it’s a dead weight. There is a physical limit to how much fuel an aircraft can carry because this overall weight limits the range.
This is why electric aircraft don’t work over 200-250 miles.
Because where aviation fuel turns into energy and exhaust gases (that are expelled overboard) – the weight of the battery remains after the stored energy is used.
SAF Pathway | FeedStock | Emissions Reduced | Pros / Cons |
---|---|---|---|
HEFA - Hydroprocessed esters and fatty acids | Used fats. Oils. Greases refined into fuel (HEFA-SPK) | Could reduce GHG by up to 80% (Life cycle basis compared to fossil fuels) | Pros: Mature Tech widely used. "Cheapest" of the SAF types. Cons: Feedstock availability issues. Vulnerable to supply chain pressures. |
ATJ - SPK - Alcohol to Jet Synthetic Paraffinic Kerosene | Alcohols like Ethanol & Butanol are de-oxygenated into fuel using a patented process | Could reduce GHG up to 80% (Life cycle basis compared to fossil fuels) | Pros: Mature Technology / Capital easy Cons: High "opportunity cost" to sell to alternate modes (road) |
FT-SPK & FT-SKA - Fischer-Tropsch Processed | Municipal solid waste and forestry waste are converted to fuel with a patented process | Could reduce GHG by up to 80% (Life cycle basis compared to fossil fuels) | Pros: Higher blend rates with JetA1 possible Cons: Feedstock availability issues & supply chain issues. |
CHJ - Catalytic hydrothermolysis Jet fuel | Plant & Algae Oils converted to fuel by hydrothermolysis | Could reduce GHG up to 80% (Life Cycle basis compared to fossil fuels) | Pros: Suitable for Wet Biomass processing Cons: Technology immature |
PTL - Power to Liquid | Ultimate renewable energy - Water and Carbon converted to fuel via electrolysis | PTL fuels (eFuels) could reduce greenhouse emissions by 90% | Pros: Huge supply / Feedstocks. Very clean fuel Cons: Energy intensive. Requires clean electricity & Carbon capture |
ASTM D7566
For those of you with more formal or regulatory leanings and want to know what governs all fuel (including SAF) you need ASTM D7566. You can go directly to the Specification standards at ASTM. But this is what controls the quality of all fuels.
Turbine engines are extremely sensitive to the hydrocarbons that fuel produces. It affects the performance of the engine and its life between shop visits. Owners, Airlines, and Insurance companies care deeply about the issues of fuel, especially when we start to blend it with SAF.
IATA for SAF
And for that reason, it is IATA that has taken on the mantle of SAF for airlines. SAF (and Biofuels) have been used since 2000 and the first full Biofuel pathway was approved in 2009.
But all industries want sustainable fuel. Especially those that emit the most CO2 by volume such as Industry, shipping, and trucking. So, the pathways are inundated with demand and competition. And production speeds are not where we need them to be. Yet.
WEF Report 4 Pathways to SAF
According to the World Economic Forum (WEC) “Clean Skies for tomorrow” report, there are four pathways for SAF:
- Hydroprocessed fatty acids esters and fatty acids (HEFA)
- Gasification/Fische-Tropsch (FT)
- Alcohol-to-Jet (AtL)
- Power-to-Liquid (PtL)
HEFA is by far the most productive and established method. Most production sites are based in North America and Europe, but Neste in Singapore will soon become the biggest producer by volume.
There are 100 other production sites planned according to ICAO and it is hoped that this would deliver enough SAF raw material to meet the 2050 demand. But there is an issue, raw material demand.
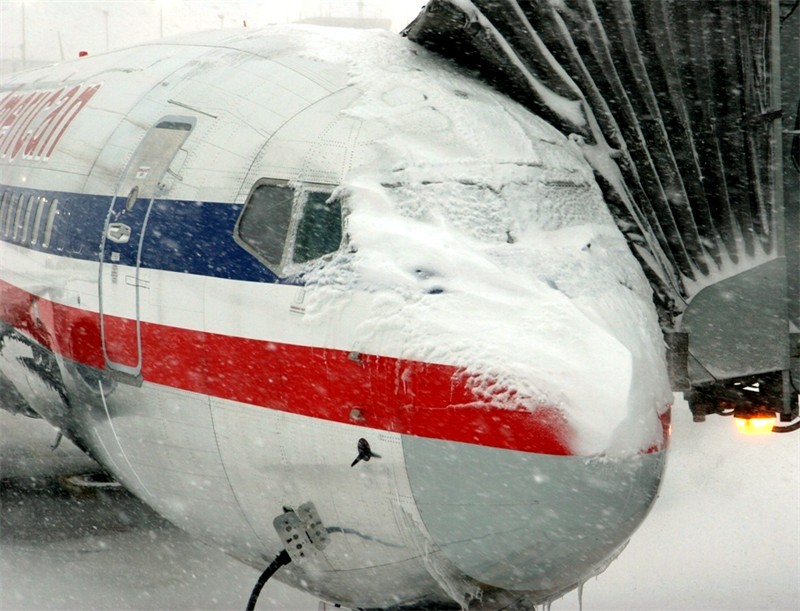
Raw Material Demand
The raw materials for SAF production vary, but they mostly include
- Used Cooking oils, animal fats
- Municipal waste
- Forestry/Agricultural waste/residue
- Rice/Cereal production residue
- Purposely grown energy crops/Biomass
- Captured Carbon
But SAF is not the only channel demanding raw material. All other sectors needing fuel to deliver, build, make or transport are seeking these same materials.
For now, meeting our SAF commitments by 2050 is a challenge. The hope is that as other energy sources mature (such as Hydrogen and Electric for trucks and ships) these raw materials will be freed up for SAF production.
SAF Cost
Fifty percent of the total commercial flight costs are fuel. So, Airlines and You (the price-Googling public) are the beneficiaries, or victims, when the price of fuel goes up.
The cost of producing SAF is significantly higher than traditional aviation fuel. HEFA, the most common and productive method, as an example, costs 200% more. Of course, the price should be reduced as production (and competition increases), but it is unlikely that SAF will reach parity with Jet fuel and is estimated to always be 100-150% higher. Our passengers will pay for that.
However, as the costs of carbon and carbon-pricing increase in the years to come, SAF should reach parity in the future.
Top SAF Producers
SAF Pathway | FeedStock | Emissions Reduced | Pros / Cons |
---|---|---|---|
![]() | Neste | Finland, Holland, Singapore | NEXBTL Technology |
![]() | Fulcrum Bioenergy | USA, UK | Fischer-Tropsch Technology |
![]() | SkyNRG | Holland, USA | Biomaterial Production |
![]() | World Energy | USA | QuestZero |
![]() | Air BP | Worldwide | Biomaterial Production |
![]() | Shell | Worldwide | Biomaterial Production |
ATAG Waypoint Report
So which airlines on board for SAF?
IATA has committed its members to 5% SAF by 2030. Seventy other world airlines have also committed to “some” SAF usage by 2030. In total, 50% of the world’s airlines have committed to net zero by 2050.
But as you can see, the production and delivery of SAF depends on many key factors. Most of which are outside the control of aviation stakeholders.
We have an offset market where Airlines, like other companies, purchase credits for CO2 emission overages. But there are concerns and doubts about the long-term viability of this process.
A good source of information is the Air Transport Action Group’s Waypoint 2050 report. Put simply there is a variety of actions that are needed by all stakeholders to play their part. Which include you. The report details how;
- The Energy Sector driving Investment and scaling
- Airlines committing to Offsets
- Passengers paying “green” premiums
- Government incentives
- Grants and Schemes for SAF production
- Financiers and Investors for SAF, Hydrogen and related Technology
Aircraft & Engine design Innovations
#NetZero2050
New Engine Innovations
Green Articles
Navigating the Skies: Exploring Flight Information Regions (FIRs)
Boeing 797: A Sustainable Future for Aviation
Sustainable Aviation Fuel – The SAF Bet
How to Improve Diversity & Inclusion in Aviation
CORSIA – Carbon Credits and Offsets in Aviation
Why Hydrogen as Propulsion?
Hydrogen contains Zero Carbon. And so, no CO2 is emitted when combusted. There is also the absence of secondary emissions compared to kerosene such as carbon monoxide, unused hydrocarbons, soot and other organic compounds.
Water and Nitrogen Oxides are the key emissions. And both are bad. Water at high altitude is a greenhouse gas for example (albeit over 10km). However, the N0x is lower than kerosene by the order of 45%.
How is it done?
Hydrogen can be used as aviation fuel via two methods.
- Combusted in a Turbine Engine (like traditional fuel)
- Used in Fuel Cells – which generate electricity – driving electric propellers or propulsor
It is agreed that Fuel cells are best suited for short and medium haul aircraft solutions whereas combusting Hydrogen is best for long-haul widebody aircraft. If we can build them. Which we will need to, due to the design challenges when using Hydrogen as fuel.
SED v VED
To understand these challenges, we need to understand the differences between Hydrogen and Kerosene. And we do this through Specific Energy Density (SED) and Volumetric Energy Density (VED).
Jet A-1 has good SED and VED. That is, it delivers sufficient energy for both weight and volume. Weight and volume being key aircraft design factors.
Hydrogen Gas is more voluminous than Kerosene if we expect it to deliver the same SED parameters. Its VED is 0.01MJ/L compared to 35MJ/L of Kerosene. So, we must convert Hydrogen Gas into liquid – where it approaches the VED of Kerosene. Here we have two options.
- Pressurized Tanks (Difficulty level: High)
- Cryogenic Tanks (Difficulty Level: Extremely High)
Why? Cryogenic Hydrogen must be kept at -235 Degrees Celsius and we need fuel space in the order of 4x to compare to Kerosene.
There is a huge upside, however. The Weight of Liquid Hydrogen is only one-third of kerosene for the same energy output. So, if we can pull this off, the range of these new aircraft (combined with some speed increases) would transform commercial aviation, for almost zero emissions.
Aircraft Design Changes for Hydrogen
-235 Celsius. Yeah. Not easy. Now it’s not all bad news. Aircraft need heat-sinks. All aircraft use cold fuel to combat the heat generated in other aircraft systems such as hydraulics and electrics and air-conditioning packs. So, the designers and makers of these systems will welcome this.
Getting safe, well-insulated, Cryogenic tanks into an airframe and having that same airframe deliver this liquid to turbofan engines for combustion is something else entirely.
Here are some of the Key Design challenges when working with Cryogenically stored Liquid Hydrogen for aircraft use:
- Tank(s) Size/placement (aerodynamics)
- Heavy Tank Insulation (weight/safety)
- Venting is needed due to the expansion of Hydrogen (safety)
- Traditional Aviation structural metals become brittle when exposed to these temperatures (fatigue).
- Hydrogen seeps. Even through microscopic pores in metals and welding (safety).
- Airports and Fuel farms will need to manage and design delivery equipment (Innovation/Safety)
- Aircraft refueling and containment (safety).
It has been agreed that the BWB (Blended Wing Body) represents the best aircraft design solution for Hydrogen propulsion. OEM’s are already in research mode. Boeing and NASA have had a look but don’t seem to want to go down that road. But a company called JetZero is. But we are only beginning to dip our toes into this pool of discovery. And new and open minds are needed.
Key Benefits & Challenges
If we are to reach Net Zero, we are limited in the substances that we can use. Hydrogen fits the bill better than anything else. Especially for medium and long-haul travel where electricity doesn’t work.
Hydrogen also has an improved combustion range and flammability limits compared to kerosene. Its combustion instability profile is also lower when compared to other options.
But producing Hydrogen Liquid is also difficult. And expensive. And our ability to produce it En-masse is nowhere near where we need it to be. So, it is a solution for the period after 2030. And that is if we can solve the design challenges posed by liquids at these temperatures on aircraft with passengers and crew at 35,000 feet.